Temperatures totally wrong 3.4 RC
-
@hernicz said in Temperatures totally wrong 3.4 RC:
If you have a copper heatblock, at initial heatup it way overshots temp. The purpose of PID is to precisely reach target temp and sustain it in a changing environment. But when you use copper, heatup just doesn't slow down. It's like PID is hardcoded to aluminium heatblock.
This is not true in my experience. I had E3D v6 copper block (with copper nozzle and titanium heatbreak) in my delta from new and had no problems with a number of v3.4 betas and RC1 & 2 on a MB6HC. All tuned fine (as tools, not heaters) and worked fine when tuned. So it's not the case that something fundamental in the tuning cannot accomodate a copper block.
I'm now using a Revo, so the concept of block dissapears somewhat, since there's heater - nozzle assembly without discrete block. FWIW, that has tuned fine too.
-
@hernicz this post? https://forum.duet3d.com/topic/26830/issues-with-pid-tuning-rrf-3-4-0-b7/
I’ll try and get @dc42 to look at all threads where PID tuning is an issue. If you spot more, please post them here. Maybe if they’re taken all together there may be a common issue that he can look at.
Ian
-
@droftarts said in Temperatures totally wrong 3.4 RC:
@thedragonlord okay. Can you at least post the M307 you were using in 3.3? Then we might be able to reproduce the issue.
For now I’ll update the M303 instructions to say that if the feedforward isn’t working for the user, to tune heaters rather than tools, as @Hernicz suggests.
Without sufficient data and information to be able to understand the cause of issues and to reproduce them, it’s very difficult to resolve them.
Ian
I've been not using 3.3 but 3.4 beta 6 but unfortunately I have no backup for the files...
-
@thedragonlord in the 3rd post in this thread, when running RC1, your M307 was
M307 H1 R2.033 K0.194:0.179 D6.99 E1.35 S1.00 B0 V23.9 M307 H2 R1.889 K0.191:0.164 D8.45 E1.35 S1.00 B0 V23.9
That’s the format for 3.4beta7 and later. Are you are using these in 3.4beta6? If you’ve retuned and it’s working, please post what you’re currently using in beta6. Then we can at least compare the computed PID values for each method, to see where it differs.
If you’re now on RC2 and you retuned just the heater not tool (as it would seem from your other posts), and it’s working, post that, so again we can compare the PID with the non working tune.
Ian
-
@droftarts Yes, that's it.
-
@achrn I also have 50W heater running at 30V, but Voltage was taken to account.
I'm not the only one with this issue. Are you running on SBC or standalone?
-
@hernicz SBC
I'm not claiming you're not having problems, I'm saying the assertions that "If you have a copper heatblock, at initial heatup it way overshots temp" and "when you use copper, heatup just doesn't slow down" are not universally true.
I don't understand why voltage is relevant, if you tune at (near) the voltage you run at (and if you don't, then I think you should).
-
@achrn I mean after tuning the copper heatblock, heating up from room temp overshot it until triggered a heater fault. Like it didn't know when to slow down heating to reach target temp. It seems like PID tuning doesn't tune for heat up from ambient, only to hold target (yet it cannot even do that if you calibrate tool with cooling fan)
It may not be universally true, but I don't think any PID tuned heater should behave like this. The whole point of PID tuning is to eliminate this (and have a steady target temp).
I had a copper volcano heatblock with a 50W heater and copper nozzle. I don't have issues with aluminium heatblock.
SBC as well. Voltage is just additional info, may not be relevant.
-
I wrote down my values.
What can I do to get rid of these fluctuations?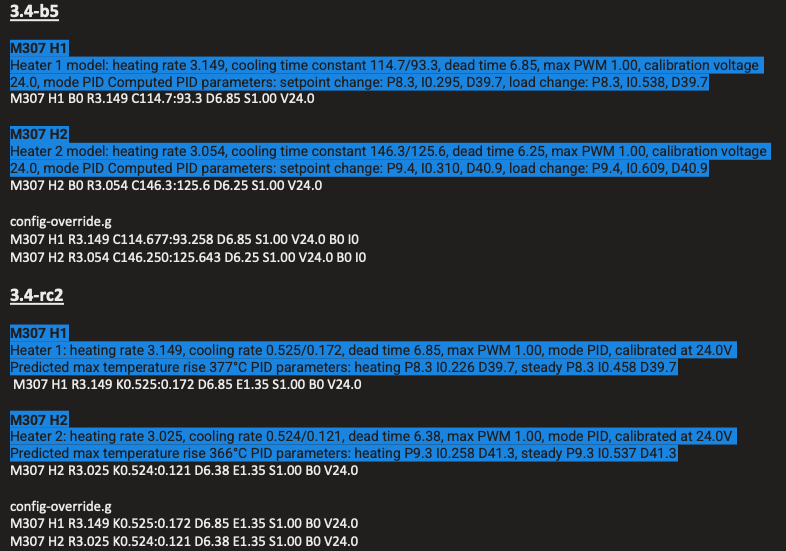 code_text ```3.4-b5 M307 H1 Heater 1 model: heating rate 3.149, cooling time constant 114.7/93.3, dead time 6.85, max PWM 1.00, calibration voltage 24.0, mode PID Computed PID parameters: setpoint change: P8.3, I0.295, D39.7, load change: P8.3, I0.538, D39.7 M307 H1 B0 R3.149 C114.7:93.3 D6.85 S1.00 V24.0 M307 H2 Heater 2 model: heating rate 3.054, cooling time constant 146.3/125.6, dead time 6.25, max PWM 1.00, calibration voltage 24.0, mode PID Computed PID parameters: setpoint change: P9.4, I0.310, D40.9, load change: P9.4, I0.609, D40.9 M307 H2 B0 R3.054 C146.3:125.6 D6.25 S1.00 V24.0 config-override.g M307 H1 R3.149 C114.677:93.258 D6.85 S1.00 V24.0 B0 I0 M307 H2 R3.054 C146.250:125.643 D6.25 S1.00 V24.0 B0 I0 3.4-rc2 M307 H1 Heater 1: heating rate 3.149, cooling rate 0.525/0.172, dead time 6.85, max PWM 1.00, mode PID, calibrated at 24.0V Predicted max temperature rise 377°C PID parameters: heating P8.3 I0.226 D39.7, steady P8.3 I0.458 D39.7 M307 H1 R3.149 K0.525:0.172 D6.85 E1.35 S1.00 B0 V24.0 M307 H2 Heater 2: heating rate 3.025, cooling rate 0.524/0.121, dead time 6.38, max PWM 1.00, mode PID, calibrated at 24.0V Predicted max temperature rise 366°C PID parameters: heating P9.3 I0.258 D41.3, steady P9.3 I0.537 D41.3 M307 H2 R3.025 K0.524:0.121 D6.38 E1.35 S1.00 B0 V24.0 config-override.g M307 H1 R3.149 K0.525:0.172 D6.85 E1.35 S1.00 B0 V24.0 M307 H2 R3.025 K0.524:0.121 D6.38 E1.35 S1.00 B0 V24.0
-
-
@Hernicz
M307 H1 R3.149 K0.525:0.172 D6.85 E1.35 S1.00 B0 V24.0you mean like that?
M307 H1 R3.149 D6.85 E1.35 S1.00 B0 V24.0
-
@jensus11 said in Temperatures totally wrong 3.4 RC:
@Hernicz
M307 H1 R3.149 K0.525:0.172 D6.85 E1.35 S1.00 B0 V24.0
you mean like that?
M307 H1 R3.149 D6.85 E1.35 S1.00 B0 V24.0No, leave in the first K parameter, so like:
M307 H1 R3.149 K0.525 D6.85 E1.35 S1.00 B0 V24.0
Ian
-
-
I don't think that was the case in 3.4-b5. It is not possible for me to print a Temptower. The temperature is just fluctuating. With other parts I noticed that the temperature increases in the first layer of the top layer after the infill part.
If I reduced the Bridges fan speed, it's better. I think when the part fan changes fast and slow the fluctuating start. If the partfan is constant, the temperature is also constant.Tell me what to do to help.
100% Bridges fan speed in my test print
50% Bridges fan speed in my test print
should i upload the gcodes?
-
It really must be the transition from infill to top layer. If I only print the botton and then the top layer, it's ok. Exactly the same if I only print perimeter.
-
@jensus11 please try with the second K parameter in the M307 command missing or set to zero, as @droftarts suggested. This will help me to pin down the problem.
-
I am running tests on one of my machines with a new hot end installed, and although the behaviour I am seeing is nothing like as bad as reported in this thread, it is evident to me that the heater feedforward when fan PWM is changed is not working correctly even though the M307 parameters appear to be correct. I will continue investigating tomorrow.
-
I just found the bug that is causing this. I will provide updated RRF builds tomorrow or Wednesday. Meanwhile you can set the second M307 K value to zero to disable feedforward.
-
@dc42
I tested it without the second K value. It's better but not good yet. With K0 it looks very good. -
@jensus11 @Hernicz @resam @TheDragonLord I've put 3.4.0rc2+2 binaries at https://www.dropbox.com/sh/amtiizdcylnuaye/AAA4hzXFvU0RMOSDtdT37HFua?dl=0 for testing. These should fix this issue. Although the changes are minor, please test them with care.